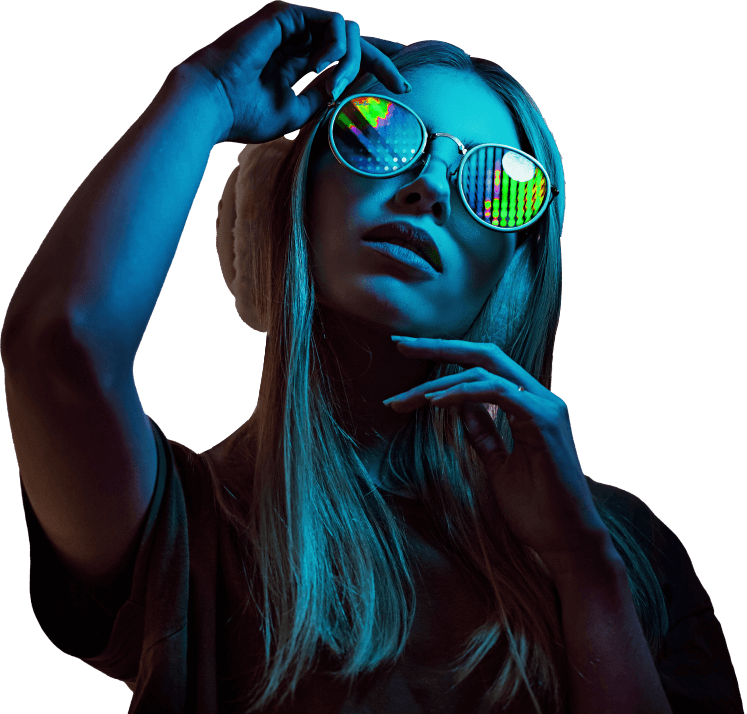
Leading the digital transformation of the fashion supply chain
Business critical garment software and fashion industry expertise, powering an agile, resilient, transparent and sustainable supply chain
Optimise. Connect. Accelerate.
Coats Digital’s business critical garment software solutions embedded with deep industry expertise and proven to digitally transform the way fashion companies design, develop, cost, plan and manufacture. Our fashion supply chain software harnesses industry best practices and the latest technology to improve speed to market, agility, efficiency and sustainability, and are trusted by brands and fashion manufacturers around the world.
What we do
We simplify complexity
In an increasingly volatile, uncertain and complex world, in which speed, efficiency and sustainability are terms of trade, we enable fashion businesses to meet these challenges by focusing on simplifying and optimising key business processes which have disproportionate impact on performance.
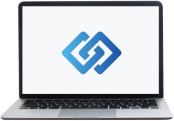
How we do it
Transformational technology and fashion industry expertise
Specialist, business critical solutions, created for the fashion industry and proven to deliver significant, measurable and sustainable improvements in operational and financial performance, while concurrently delivering on CSR commitments.
Who we work with
Specialist solutions for fashion brands and manufacturers
Fashion Brands
We help brands and their supply chain partners to optimise, connect and accelerate the entire product development, costing, sourcing, planning and order execution lifecycle.
Fashion Manufacturers
We help manufacturers transform business critical processes, from design and development to method-time-cost optimisation, production planning and control, fabric optimisation and shop floor execution.
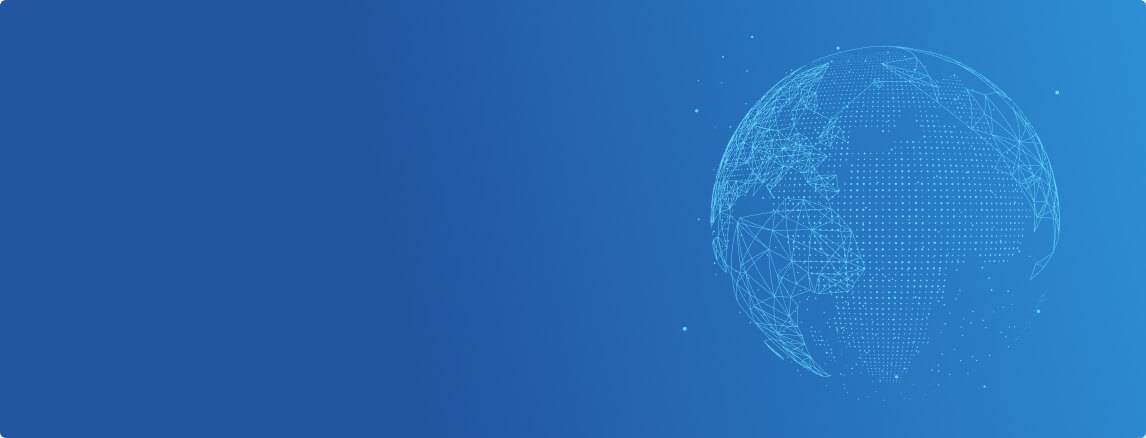
It’s time to transform your fashion business
Delivering real results
What our customers say
South East Asia
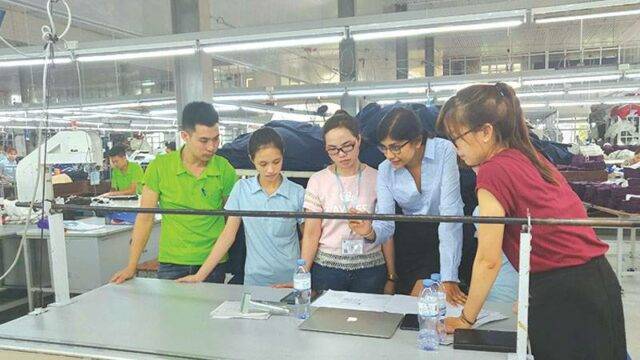
#FabricOptimisation
FastReactFabric (formerly Intellocut) helps Song Hong to reduce 60% of fabric planning time
FastReactFabric accounts all the wastages on the cutting floor and reconciles the data in the reports for any desired date…
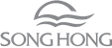
South East Asia
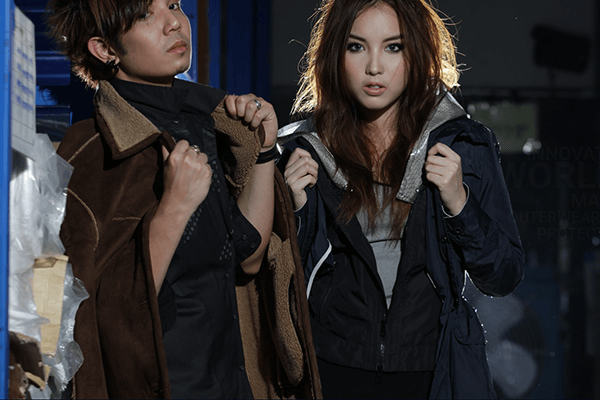
#ProductionPlanning
VT Garment Improves Productivity by 95% & OTDP by 50% with FastReactPlan
The adoption of FastReactPlan helped VT Garment secure the prestigious ‘Golden Award’ at the ‘Thailand Lean Award 2017 in recognition…

Europe, Middle East, and Africa
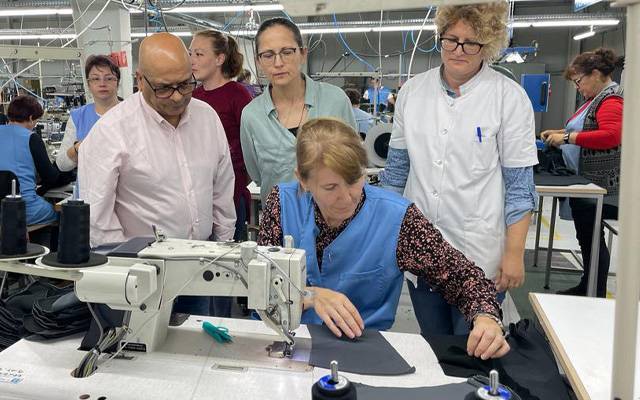
#MethodTimeCostOptimisation
Sportswear brand, ODLO, increases productivity by 10% with GSDCost
By establishing accurate Standard-Minute-Values, GSDCost has enabled ODLO to optimise profit margins, secure new business and enhance team members’ motivation…

The latest industry and technology updates
Industry insights
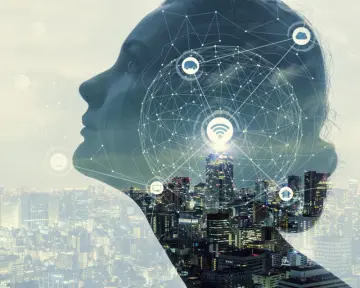
#SupplyChainSolutions
Cloud Artificial Intelligence (AI) providers and the huge potential they have for Enterprises
This article discusses how to build rules and regulation validation system using traditional programming along with artificial intelligence (AI). Objective…
Read more
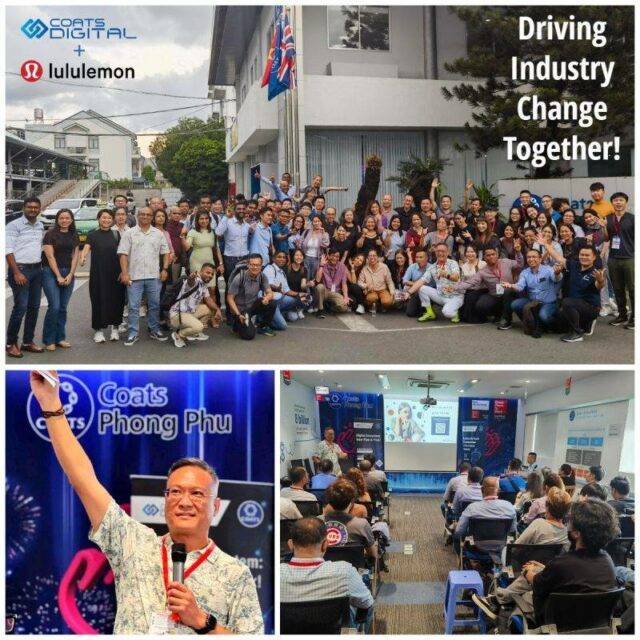
#MethodTimeCostOptimisation #Sustainability
Insightful event alongside Lululemon!
Hybrid event at Coats Phong Phu Factory discussing how to build a more profitable and sustainable relationship between brands and…
Read more
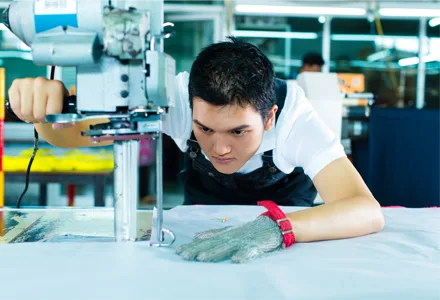
#FabricOptimisation
7 tips for better Fabric Cutting Room Productivity
With the help of automation, the cutting room has become one of the most advanced departments in an apparel manufacturing…
Read more