Fabric is Fundamental to Fashion Manufacturing’s Fortunes
by Silky Prajapati

In this new era of superfast fashion, there is no doubt that fashion manufacturers are having to pull out all the stops in order to remain profitable.
With more countries opening their doors to offer the cheapest needle and labour prices, it has become increasingly important for apparel manufacturers to remain sharp, agile and on top of their game. In the current era of fast fashion, the number of styles per season is only going to increase. Whilst always running against the clock, therefore, manufacturers must not only deliver on time and adhere to robust quality standards, but also ensure they remain profitable, competitive – and sustainable!
As a result, it has never been more imperative that fashion manufacturers aim to optimise costs at every stage of the production lifecycle. However, with 50-60 per cent of total manufacturing outlay attributed to fabric costs, manufacturers that digitize and optimise their fabric-related processes, will undoubtedly be the biggest winners in the quest to deliver quality, ODTP and increased profitability – fast.
A manufacturer’s largest investment is at the fabric booking stage. From the initial order, they need to estimate and book the amount of fabric required to fulfil the order quantities asked for by the buyer. Since this is the stage that has a major impact on the overall cost, it is, therefore, vital to estimate accurately and on time.
Being precise with your fabric order is not only important for your profitability – it is also a key factor in ensuring you hit sustainability targets increasingly demanded by brands and consumers.
Most manufacturers order extra fabric to cover any potential production losses and to avoid short shipments. Brands also often commission more yardage than necessary to cover these potential production losses. There are numerous other reasons that can lead to an accumulation of dead stock at the end of a season – which simply cannot be used further in more styles. Nonetheless, there are only two roads where this unusable dead stock eventually ends up. It either gets incinerated or is dumped in landfills. And these outcomes are not at all in harmony with global sustainability drives and increasing legislation to reduce waste and pollution in the bid to save our planet.
The fashion industry is said to produce 92 million tons of solid waste each year[1] that significantly contributes to air, water and land pollution. Apparel manufacturers must, therefore, make more conscious efforts – backed up by real action – to ensure that only the required amount of fabric is produced in their garment manufacturing processes.
But how can a manufacturer ensure it estimates the right amount of fabric quickly and easily? Historically, the standard process still followed by many apparel manufacturers to achieve this includes: the creation of patterns in CAD according to the techpack; the setting of standard ratios (cutplan) to fulfill order quantity; the creation of markers in CAD according to agreed ratios to get the marker consumption; the inclusion of buffers and allowances to preempt variances in on-floor processes and finishing; and finally an overall assessment of the booking consumption (factoring in marker consumption and buffer allowance) to estimate the final fabric amount required.
As simple and linear as this process may look, we still know that most manufacturers struggle with issues of dead stock lying in their inventory or have to re-order fabric at the last minute, to avoid short shipments.
The key problem here is the consumption ‘gap’ that is created between booking fabric and the actual utilised fabric on the floor. If manufacturers can reduce the consumption gap by even a small percentage, this would inevitably lead to significant profit margins, whilst helping the planet by reducing fabric wastage, at the same time.
The major components that make up the fabric requirement are the consumption of the garment and the buffer applied on top of it. The two major factors that affect these components are – data and time.
Reduced Lead Times are Vital
If time was our best friend, everyone would follow the best process possible to estimate – marker consumption – a production grade cut plan detailing a 100% order quantity to base all markers required. Most accurate marker consumption can only be estimated if all constraints that would be used in the production stage, are applied at the buying stage as well. This factor is key, since any variance during estimation and actual cutting, such as pattern buffer, layout etc., will create gaps in the booking and cutting consumption, which would lead to unnecessary fabric wastage, or conversely, fabric shortages.
Unfortunately, not many manufacturers have enough time to follow each step this way, for every style. Ultimately, if they are not supported by technology, this process will remain a mammoth task, which is unlikely to hit the bullseye in the notoriously limited lead times they have to work against.
A lack of insightful data always leads to inaccurate fabric estimates
Insufficient data during fabric estimation is one of the key reasons why manufacturers end up with short or excess fabric by the end of the order completion. In most cases, at the time of fabric booking, the size quantity breakdown is unknown. Most manufacturers cannot afford to wait for this – since the clock is always ticking. They consequently usually rely upon standard ratios that are expected to come from the buyer to create the marker and derive marker consumption.
If the marker/marker consumption is not known nor provided by the buyer at the time of booking, the best practice is to go back and look into earlier orders executed for this buyer – for the same product, style and fit, and then predict the expected size breakdown using past trends. This is often as close as many manufacturers can get to predicting a marker consumption statistic.
In addition, the same historical data must also be used to estimate the buffer/allowance that is applied over the marker consumption to ensure sufficient fabric is booked. Instead of following a standard buffer, using the factory’s own historical data is certainly the right way to go. The amount of fabric that has been consumed or wasted in various other processes in similar historical orders, can help estimate the expected wastage in the new order. Once again all you need to do is look into your own data to scientifically back up your estimation process – to get one step closer to reducing that illusive consumption gap.
Ultimately, manufacturers will only be able to effectively reduce their consumption gaps if they bring onboard the relevant technology solutions to provide the data and meaningful insights required to make effective decisions. If you’re not supported by technology, then you will remain in an outdated, analogue world that will eventually render you not fit for purpose in the fast-approaching future. With consumer demand for fast fashion and greater style variety, manufacturers that continue to scramble for historical style and fabric data across a myriad of computer sources, will simply run out of time and will never meet or beat that forever ticking clock.
Coats Digital has been helping fashion manufacturers automate and optimise the estimation of fabric consumption for years.
However, with fabric optimisation and wastage reduction being such a business-critical element of garment manufacturing today – Coats Digital’s FastReactFabric, uniquely connects your fabric buying and fabric cutting operations into a single platform to accurately procure and utilise fabric.
References:
- As per a study by the Ellen McArthur Foundation
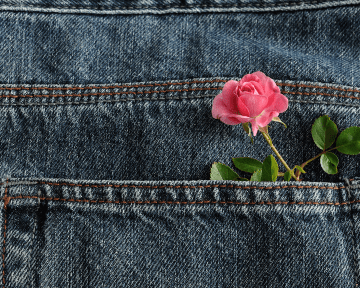
Embracing Circular Fashion: A Sustainable Solution for the Apparel Industry
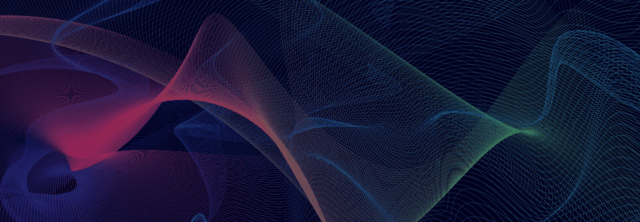
Digitization – Practical Steps for Garment Manufacturers
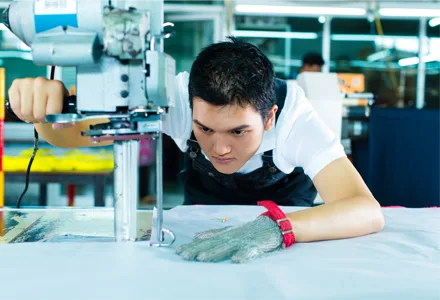
7 tips for better Fabric Cutting Room Productivity
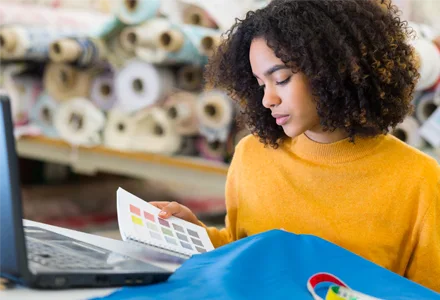
Smart fabric buying: Necessary steps and challenges
All Blog Categories
- Fabric Optimisation
- Sustainability
- Corporate
- Design and Develop
- Method Time Cost Optimisation
- Production Planning
- Shop floor execution
- Supply Chain Solutions
- Videos