Understanding PMTS in the Garment Industry
by Coats Digital

The readymade garment industry is highly labour-intensive. Hence, labour cost per hour is an important factor in this sector to remain competitive. We can safely consider labour costs as one of the highest cost factors in the readymade garment industry.
Assembly line production system has made it important that work done by each production worker is measured in terms of “method” and “time”. This work once measured is then standardised and rationalised for a consistent and accurate output with optimum labour expenditure. Each worker needs to be assessed based on the standardised output parameters so that manpower is effectively planned, and daily output planning can be done in advance.
Also, such information provides the management to assess the effectiveness of people and machinery employed within the business along with the means for management to increase productivity.
Garment manufacturers all over the world catering to high fashion markets are in tremendous pressure to deliver products in a shorter manufacturing lead time. Garment exporters typically work with a lead-time of 75-90 days, vertically integrated plants are known to work with even longer lead-times. With turnaround time becoming a prime factor in attracting business, manufacturers are increasingly exploring options to reduce the cycle lead-times. Any delayed shipment would affect the credibility of the vendors and decrease their profitability.
The onus is on manufacturers to create an efficient Time and Action Calendar (T&A) plan for a style order that is successfully executed without any delay. It is important for a garment manufacturer to cost a garment with a high level of accuracy prior to the start of the production process. Deriving a labour cost at the time of order booking is a challenge which affects both the manufacturers and brands. Mostly the CM cost derived at the costing stage is not very accurate since there are no set standards followed to derive the same.
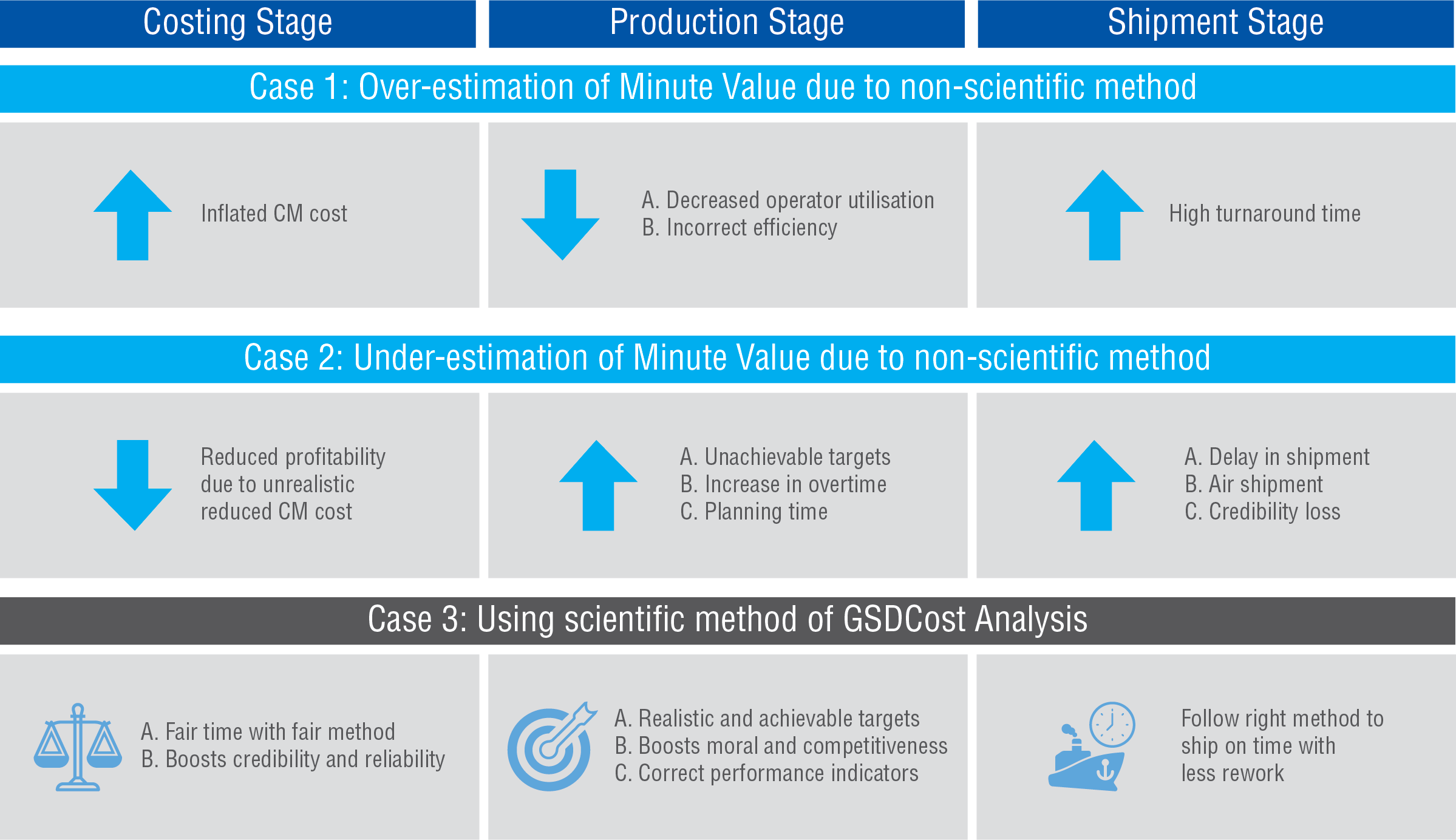
About Time Study and how its limitations were catered by MTM Core DataTM
Garment manufacturers have been using time study to estimate labour cost and labour performance on the floor. Time Study required the practitioner the use of a stopwatch, usually calibrated in 1/100 of a minute and be competent at Rating Operator Performance. The practitioner is required to observe and time an operator while the operator is performing the specified tasks. The Rating process requires that individual practitioner to fully understand the level of skill and speed necessary to complete the task at predefined levels of proficiency.
What is MTM Core DataTM ?
MTM Core DataTM is a Flexible, Multi-Level, Predetermined Time Standard that can be entered at any level in order to achieve the level of accuracy required by the user.
The aim of Core Data was to provide a predetermined time standard system which retained all the analysing power of the MTM-1 and MTM-2 systems and which could also define the work cycle, whether constant or variable, with a single motion pattern.
Below are some of the limitations seen while working on the Time Study which is now catered by MTM Core DataTM system:
- Time study is dependent on the ability of a person to apply accurate, consistent and objective Performance Rating. This inability could lead to inaccuracy and inconsistency in the set standards.
- Time study alone is not possible to maintain standards where workers are given wages on the basis of the number of garment pieces they make.
- Time Study itself takes up time to apply and the cost to individual businesses in employing Time Study Officers is extensive as many hours are spent in proving time standards.
Yet the major limitation is the fact that this process was that it cannot be applied until the product is being manufactured – and by then, delivery date and costs have been agreed, so any discrepancies will undoubtedly lead to difficulties with scheduling and profitability.
Introduction to GSDCost
To make the entire process of Work Measurement by the use of Predetermined Time Standard more effective, accurate and user-friendly – GSDCost was established in the year 1978.
General Sewing Data (GSD) is subject to a continual development program by GSD (Corporate) Ltd. (now GSDCost) which is a part of Coats Digital, using the MTM Core DataTMdatabase.
GSDCost was developed using MTM core data, to provide a consistent, accurate and easy to understand, easy to communicate, methods analysis and time standards determination technique. It was designed specifically for the sewn product industry and was researched and developed within the same.
GSDCost being a software-based program automates the work measurement and analysis process reducing a lot of manual effort and intervention.
It has an inbuilt library that has time values saved for a large number of operations for a wide range of products. This library keeps getting updated with time when the user is gradually working every day, which can later be put to great use in times when a similar/same product is to be analysed again. GSDCost is bringing automation and accuracy in the lives of garment manufacturers to measure productivity in the most efficient way possible.
The latest version GSDCostV5 leverages the latest software architecture to deliver a highly intuitive SaaS solution, hosted in Microsoft AzureTM providing businesses of all sizes with fast access from anywhere to a high performance, secure, cost-effective and scalable solution. GSDCostV5 also supports open discussions and cost allowance for sustainable, fair living wages in any country to ensure high standards of Corporate & Social Responsibility (CSR) and Ethical Compliance for brand and manufacturer.
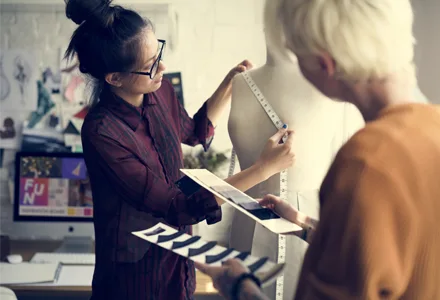
How PLM can make a difference to combat Fast Fashion
All Blog Categories
- Method Time Cost Optimisation
- Corporate
- Design and Develop
- Fabric Optimisation
- Production Planning
- Shop floor execution
- Supply Chain Solutions
- Sustainability
- Videos