Bodynits achieve a faster planning process with FastReactPlan to gain efficiency by 20%
Planning time reduced from 5-7days to 1 day. Planning became much more efficient keeping the same products on the correct lines which increased average efficiency by 20%.
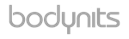
Headquartered in Singapore, Bodynits supplies the active wear sector, working with leading brands such as adidas, Under Armour, Lulu Lemon and Puma. Within their headquarters, the team focuses on product development, materials sourcing and purchasing. Due to the demanding nature of the fast growing athleisure market, Bodynits have invested in technology to ensure best practice procedures which are in place to support the entire manufacturing process. This enables them to support the synchronization of management and offshore manufacturing facilities.
20 %
Increase in average efficiency
5 − 7
day reduction in planning time
The challenge
Ms Nguyễn Thị Thu Hồng (Kitty), the Factory Manager for An Thanh, BI (VN) Co. Ltd (Bodynits’s first Vietnam factory located in HCMC), explains the challenges she faced with manual planning before using FastReactPlan (previously known as Evolve), “Our factory has 30 lines, and on average we make 80 different styles every month. Before we purchased FastReactPlan, it took me a lot of time to go through the schedule to find the best line for that product family, calculate the daily output and check status of material and sample approval. We used to spend 5-7 days to do this. It took so long just to get the data in one place!
“On top of that, the customer started to push for a much quicker order confirmation than before, so in many cases I didn’t have enough time to check everything and had to base my response on experience only. This did not always work as we could not maintain the same product family in same line, and it hurt our efficiency when workers had to change a familiar style to another.”
The solution
During 2014/15, Bodynits implemented FastReactPlan planning solution throughout the group. Having FastReactPlan connected to their Infor M3 and other MIS systems, allows the team to see their core data at head office through their FastReactPlan high level planning board, which in turn communicates with their line level planning board at each factory. The solution also includes FastReactPlan’s Material Requirement Planning (MRP) module which is also linked to the M3 purchasing and inventory data, so their factories have full visibility of material demand and supply relative to the plan and production sequence at all sites.
“By using FastReactPlan, I only need 1 day to make the plan and confirm deliveries! The system integrates all our data, including data from our other systems, in one place. We are able to focus on planning rather than manually entering in multiple data sets.”
Ms Nguyễn Thị Thu Hồng (Kitty), Factory Manager
“FastReactPlan also helps me to give a more accurate daily output target as it calculates automatically using the line capacity and efficiency by product family any time we need it for learning or style change. It is both quicker and more accurate than what we did before with Excel.”
Bodynits
Ms Nguyễn Thị Thu Hồng (Kitty) added, “Another good example of how it has helped us, is when I plan I don’t always follow the final delivery date. Sometimes to get the best efficiency and quality, I want to put 1 order into production earlier than the delivery date so I can keep the same product family running on a line. With FastReactPlan, I know if our existing material is in-house or the estimate date for arrival which will allow us to produce an order earlier.”
The benefits
Kitty summarises the benefits to her factory, “FastReactPlan is truly useful for top management to operate the factory effectively; I can easily make a plan which keeps most lines running the same product family and believe it is a key factor for our factory to reduce costs, increase efficiency and quality as our workers can keep sewing the same product for longer.”
“Another benefit is the 2 key reports that are sent to me every day; The efficiency report gives me a warning if any line is above or below the agreed target. The material status report lets me know of any material delays. I can then make sure that there is no line idling whilst maintaining the same product, in the same line.”
“As a factory manager, I can quickly identify which line is having problems and solve that problem ensuring production can run smoothly. We no longer have last minute rushes so we don’t need to split orders in to more lines to catch the delivery. All of this has helped us an increase our average efficiency by 20% over the past 2 years!”
Ms Nguyễn Thị Thu Hồng (Kitty), Factory Manager
Bodynits
Related testimonials
South Asia
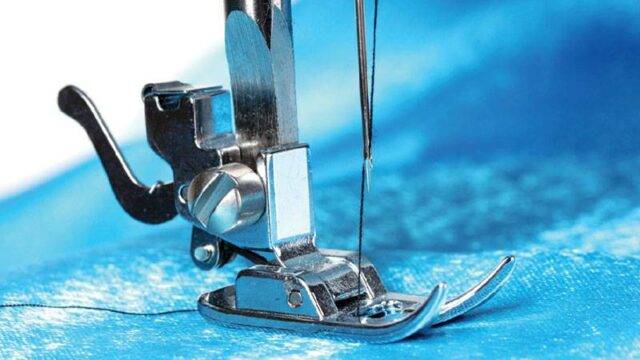
#ProductionPlanning
Brandix Group selects FastReactPlan to support strategic initiatives
As the leading apparel manufacturer looks to expand the business, they needed a solution that would strengthen their decision making…
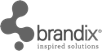
South East Asia
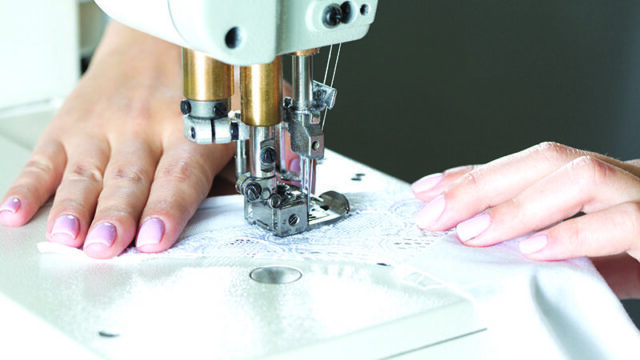
#ProductionPlanning
Busana Remaja Agracipta improves planning accuracy with FastReactPlan
Coats Digital’s FastReactPlan solution helps the lingerie manufacturer to maximise capacity utilisation and delivery performance.

South East Asia
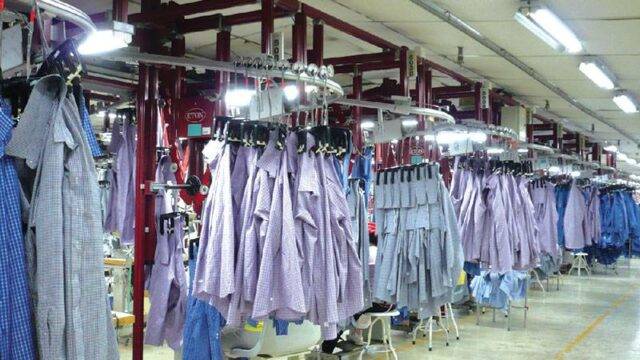
#ProductionPlanning
Esquel Group adopts FastReactPlan to support growth plan
Esquel Group turned to Coats Digital in order to centralise its capacity management and production planning capabilities across its manufacturing…
