Hojeon Improves Capacity Accuracy by 90% with FastReactPlan
FastReactPlan has also increased production line scheduling accuracy by 10%, reduced overtime costs by 5% and enabled Hojeon to accurately plan six months ahead, instead of just three.
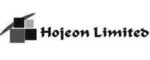
About the customer :
Headquartered in Seoul, South Korea, Hojeon is a specialist Original Equipment Manufacturer (OEM) of sportwear apparel for leading multi-national brands such as Athleta, Lululemon, Nike, The North Face, and many others. The company has developed and patented a revolutionary, high-frequency seam-attachment technology that has enabled it to produce innovative, functional, all-weather garments in a myriad of style designs. Hojeon operates seven factories across Indonesia and Vietnam and employs over 15,000 workers. It produces 1.6 million pieces a month and boasts an annual turnover of over USD 370 million.
The Challenge –The lack of a coherent capacity overview across its production sites resulted in under-and over-machine utilisation, slow production rates, poor on-time delivery performance (OTDP), and unnecessary overtime cost.
Prior to implementing FastReactPlan, Hojeon lacked a comprehensive capacity overview for all its production sites in Indonesia. Not only was capacity planning and production information fragmented across various sources in different locations, but each factory maintained its own capacity plans in Excel spreadsheets.
This decentralised approach made it challenging for the headquarters’ planning team to quickly assess the capacity availability of each factory, leading to significant time spent on collating, duplicating and aggregating records. The lack of clear visibility hindered efficient production scheduling across factories, resulting in issues such as under- and over-machine utilisation, slow production rates, poor on-time delivery performance (OTDP), unnecessary overtime costs and the lack of data insights essential for informed business decisions and growth.
“As each of our factories had their own way of planning their production runs, not having a consolidated plan made it impossible to anticipate and address potential challenges ahead of time. As planning had always been done on the basis of average line production efficiencies, the impact of slower production outputs was not obvious until mid-way through an order, leading to a constant need for firefighting. Recognising the need for a solution to meet our complex, multi-level planning needs quickly, we identified FastReactPlan as the obvious choice to seamlessly digitise our planning processes.”
Eric Kim,
General Manager,
Hojeon Limited Corp
The Solution – The complete synchronisation of the master capacity plan with detailed daily production plans has significantly enhanced productions efficiencies; increased line scheduling accuracy at each factory, and greatly reduced overtime costs.
Following the implementation of FastReactPlan, Hojeon quickly benefited from access to business-critical planning and production information from a unified digital source. This single source provided a holistic view of production capacity across all its factories, including standardised visibility into purchase orders, colour, size and delivery levels.
The enhanced data visibility and standardised format have consequently fostered cohesive and seamless collaboration across Hojeon’s production facilities. Master planners can now effortlessly assign the right jobs to the most suitable production operations, enhancing overall efficiency. Eric Kim, General Manager, Hojeon Limited Corp, added: “FastReactPlan provides us with a synchronised overview of our Indonesian factories, simplifying the management of real-time order status, product history and line scheduling. This facilitates the easy identification of factories and production lines with a positive track record of certain style processes. As a result, we can allocate jobs more effectively whilst closely monitoring how work is progressing.”
“The FastReactPlan system makes it easy to understand the data and history of a specific product. This enables us to easily make adjustments and quickly respond to changes in Repeat styles. Not only have we been able to create capacity plans in rapid time, saving considerable people hours and reducing overtime costs, but we can now proactively plan six months ahead, instead of our usual three month outlook. This proactive approach ensures stability in production costs and delivery targets, contributing to a less stressful working environment for our employees.”
Oliver Kim,
Assistant Manager,
Hojeon Limited Corp
Advancing its Digital Transformation Agenda Further with GSDCost
The implementation of FastReactPlan has been so successful that Hojeon has recently adopted Coats Digital’s award-winning GSDCost solution to establish accurate method-time-cost benchmarks that will enable its sales, costing, planning and manufacturing teams to communicate efficiently using the same language, based on a scientific method for correctly analysing manufacturing costs. FastReactPlan is the market-leading apparel production planning software solution, supporting a faster, more reliable order confirmation process and production plan which is optimised for delivery, speed and efficiency.
“We are delighted to witness the remarkable benefits achieved by one of Korea’s premier sports and outdoor clothing manufacturers following its adoption of FastReactPlan. With numerous large manufacturing plants in Indonesia, it is fantastic that Hojeon’s technology infrastructure is underpinned by FastReactPlan. We are excited to be continuing our strong partnership, as Hojeon advances its digital transformation journey with the adoption of our method-time-cost solution, GSDCost. The award-winning GSDCost solution provides scientifically-assessed cost prediction methods and practices, promising to further boost production efficiencies and drive significant financial growth. We look forward to working closely with Hojeon to ensure it meets its digitization objectives quickly.”
Irene Won,
Customer Success Manager,
Coats Digital