Jolanka optimises their Shop-Floor with Res.Q
By using the Res.Q Suite of solutions, Jolanka manages to reduce their end-line defect rate by 25%.

Jolanka began their journey in 1983 as a UK based manufacturer located in Manchester, quickly moving to set up manufacturing in Sri Lanka. The company now boasts of 4 facilities in Sri Lanka along with design, warehousing and distribution facilities in the UK. With a focus on the end-to-end supply chain, Jolanka produces over 800,000 units per month across 30 production lines. As a multi-product manufacturer, speed, agility and flexibility are at the heart of Jolanka’s operations, along with a strong focus on their associates.
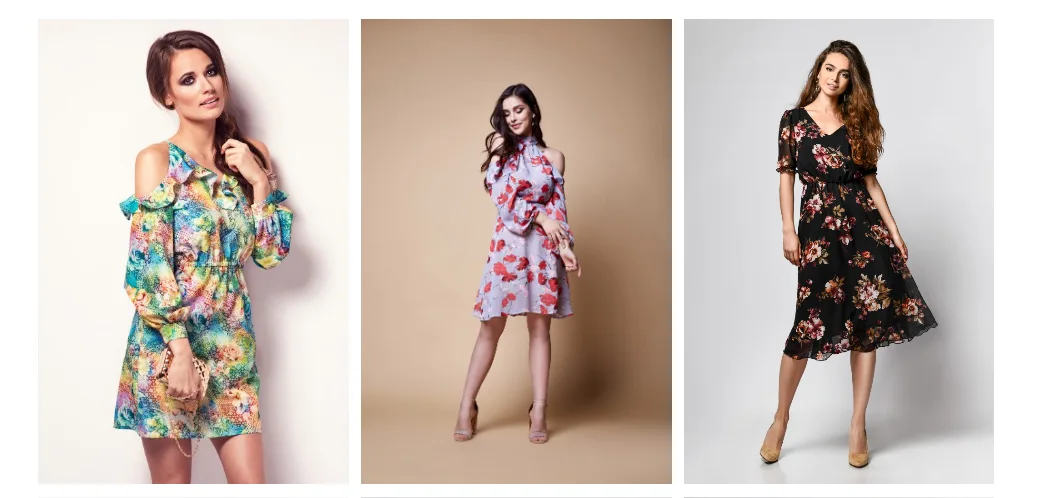
The challenge and solution
Shipping goods on time in full
In 2018, Jolanka was looking for a way to monitor their defect rates in real-time. Like in most factories, reports were done manually and often made available for review 24-48 hours later. This process was time-consuming, labour intensive and was often subject to error due to data-entry.
With increased style counts and lower quantities per style, the increased workload meant that data was often presented too late with an inability to correct the issues by the time a style was completed.
After evaluating several solutions, Jolanka opted for Res.Q | QMS. The solution was selected in order to provide real-time data, identify point of defects and to create alignment between all stakeholders within the factory and the management team.
“With RES.Q our defect rate dropped by 25%”
Denver Jayasundera, Group General Manager, JOLANKA
The end result was a reduction in end line defects of 25% enabling Jolanka to increase its On Time In Full shipments and subsequently increase customer satisfaction.
One of the key drivers of success from Jolanka was the commitment of their team. From Management through to leaders on the Shop Floor. Morning stand-up meetings are held between production, maintenance, and quality teams to ensure that the previous days’ issues are addressed within the first hour of production. Supervisors, in real time, are then able to assess products within the line to ensure that the garments are of expected quality.
With the Run Rate tracker, Production Managers are also able to review the timeliness of orders and highlight any potential delays. This enables them to prioritize resource allocation in real time.
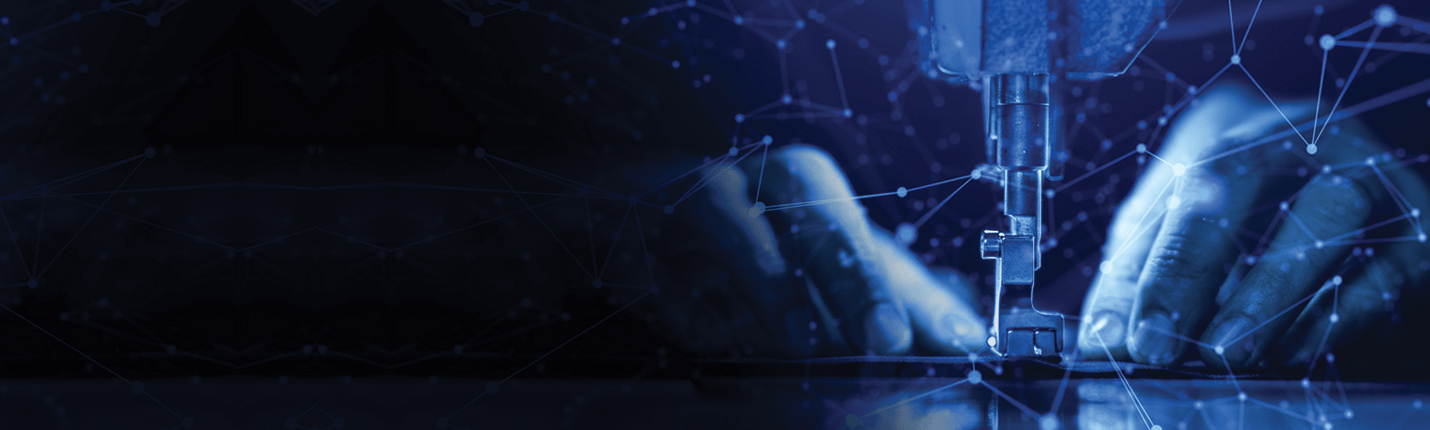
Get a Digital Copy of your Shop floor with Res.Q
Streamline processes and analyse your shop floor in real time with the industry-leading shop floor management software.
Related testimonials
South Asia
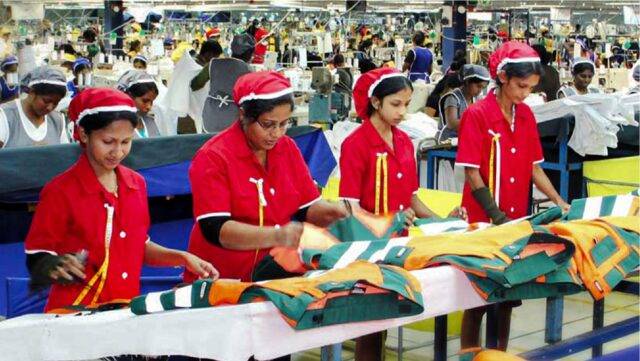
#Shopfloorexecution
GP Garments optimises their shop floor with Res.Q suite of solutions
Belgium workwear manufacturer, GP Garments empowers their team to increase productivity with Res.Q solutions.
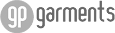
South Asia
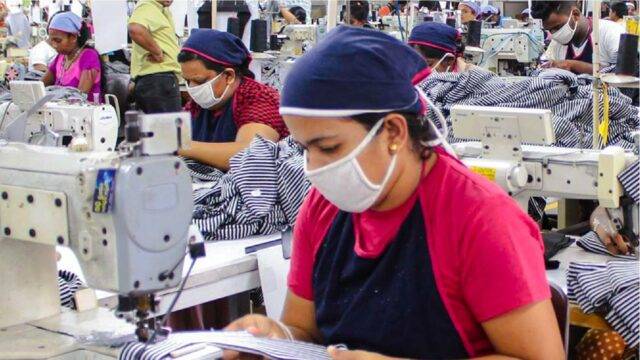
#Shopfloorexecution
Norwood Fashions gains an edge over their production with Res.Q
Norwood has lowered their defect rate and standardised quality with Res.Q shop floor solutions.
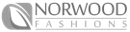
Americas
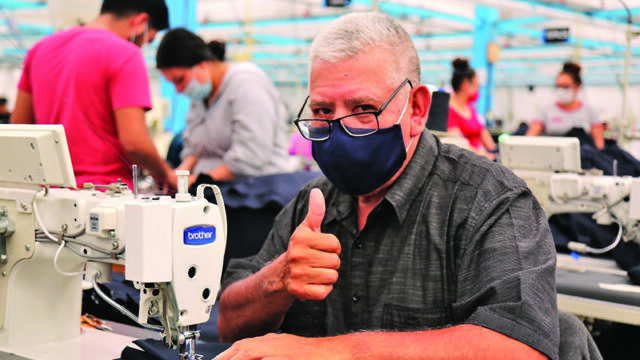
#MethodTimeCostOptimisation
Industrias Manufactureras MyR standardise method and cost
Mexico-based garment manufacturer to utilise GSDCost, to drive costing optimisation, manufacturing excellence and business profitability.
