Lim Line Apparel sees significant productivity and cost benefits by adopting ‘Best Practice’ planning
"The management team are happy to have less working hours, because we avoid the additional costs associated with OT. The overall cost reduction is around 12.5%, so everybody wins!"

Lim Line Apparel Co. Ltd. is a specialist baby wear and accessories manufacturer exporting to international brands including Carter’s, Gymboree, Janie & Jack and Armani Exchange. The company produces a wide variety of knit and woven garments and employs a team of around 4,500 across its Bangkok head office and factory, plus two factories in Cambodia.
10 − 30 %
increase in production efficiency
12.5 %
reduction in OT cost
The challenge
“For years I made the basic capacity plan and delivery promises myself. Then, my senior factory supervisor would make a more detailed sewing plan, based on her years of experience and knowledge. Reporting order status has always been a headache as data is spread around different sources and departments so decision making was time consuming and prone to errors, or missing data.
Puvadol Puriteerangkul, Assistant to the Managing Director,
However, we have always managed this way and our on-time delivery record is good; somehow we managed, but with a lot of hard work! I then became concerned when 2 big changes started to happen in our business:
1. Our key customers started requesting tighter lead times, reducing from 90 days to 60 days. I could see this would increase the risk of problems as safety time or ‘buffer’ would be reduced, with no time for any errors.
2. Secondly, we started to expand our operations to Cambodia and finding the same super – experienced supervisors there, would be a real challenge.”
Lim Line Apparel
Puvadol added: “I realised that we needed to look at improving the planning and management decision making and get a system in place, so that we did not rely on just two people’s experience and a lot of hard work. This was essential to allow us to cope with both shorter lead times and our growing business.”
The solution
Haruethai Phaleesem, SEA Business Development Manager, Coats Digital commented: “We started working with Lim Line in June 2014. They set up an all new planning team, so we helped them to establish ‘best practice’ planning concepts including the order confirmation process, adjusting output based on style mix, order size learning curves etc. These are all key to a more realistic planned output, accurate delivery promises and capacity booking. To plan accurately, you cannot use pieces and averages. Producing babywear has some specific challenges; there are many safety approval steps and a lot of product sets made up of multiple garments (e.g. hat, bib, gloves, babysuit).
So, we used many of FastReactPlan’s flexible tools such as critical path and product and order sets to be able to track individual garments and sets, as a whole, and manage the Time and Action (T&A) calendars. We also worked with their IT team to integrate FastReactPlan with their Tega ERP system, to reduce the need for manual data entry and improve the speed and accuracy of data.
Finally, we set up KPI monitoring for the senior management team to analyse progress, confirm the benefits of the planning team approach and to identify further improvement areas for action.”
The results
Puvadol Puriteerangkul, Assistant to the Managing Director, Lim Line Apparel commented: “We now think, right from the start, about how to get the best production efficiency…before, our supervisor would usually split big orders to produce in many production lines to run in short period of 2 – 3 weeks, to make sure we could deliver on time. We played safe, because we were unable to manage our line plan, predict output accurately and update the full 3 – 4 month plan quickly.
FastReactPlan has helped us to plan more accurately and has given us the forward visibility to confidently plan and produce a big order in one or two lines and still know that we can deliver on time. This brings huge benefits in terms of production efficiency and quality, as our workers get familiar and skilled at making the product on a longer run. We have significantly increased production efficiency between 10% and 30% on an order by order basis, depending on the order size.”
“FastReactPlan allows me to see everything I need to know in one place from development team updates to the latest status of main T&A activities, such as fabric ETA date, fit and pre-production sample submission dates, production sheet and packing list release, so I can check and analyse if production can start as planned.
Samrith Seebupimpa,
It’s also easy to update production every day, giving us much better WIP control to feed lines smoothly. FastReactPlan helps me to see and understand any problem areas to make sure the shipment is on time.”
Planning Manager, Lim Line Apparel
The conclusion
Puvadol Puriteerangkul, Assistant to the Managing Director, Lim Line Apparel added: “The FastReactPlan system has been easy for the Lim Line business to adopt. My team has enjoyed using FastReactPlan to replace their manual methods. The system, combined with advice from the local Thai team, has helped us to develop and improve our planning process.
We are very satisfied with the results. Now we have the ability to optimise our capacity. Our planning team really have ownership of the plan, and shout out to us quickly when they see challenges with potential underloads /overloads vs. capacity. Our sewing workers are also happy. Before they would work overtime to increase their earnings, but now they can earn the same money in a normal working day through the higher efficiency and their incentive bonus.”
“The management team are happy to have less working hours, because we avoid the additional costs associated with OT. The overall cost reduction is around 12.5%, so everybody wins! The higher efficiency and cost savings that better planning has brought us, give me the confidence that despite the higher wage costs in Thailand, we can still produce here and have a profitable and sustainable business.”
Puvadol Puriteerangkul, Assistant to the Managing Director,
Lim Line Apparel
Related testimonials
South Asia
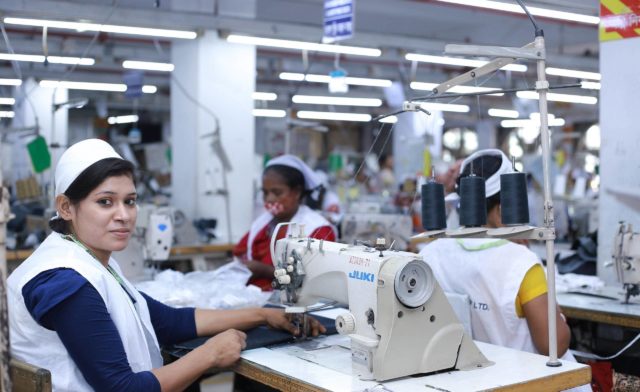
#ProductionPlanning
Azim Group increases planning efficiency by 15%
Benefits realised include higher efficiency in order confirmation time, performance to plan, cut to ship, plan & actual factory efficiencies…
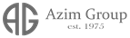
South East Asia
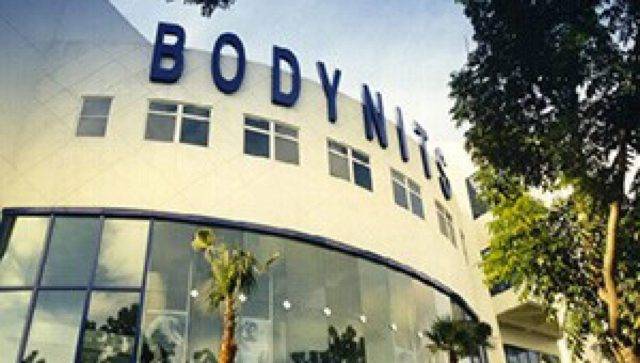
#ProductionPlanning
Bodynits achieve a faster planning process with FastReactPlan to gain efficiency by 20%
Planning time reduced from 5-7days to 1 day. Planning became much more efficient keeping the same products on the correct…
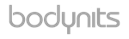
Americas
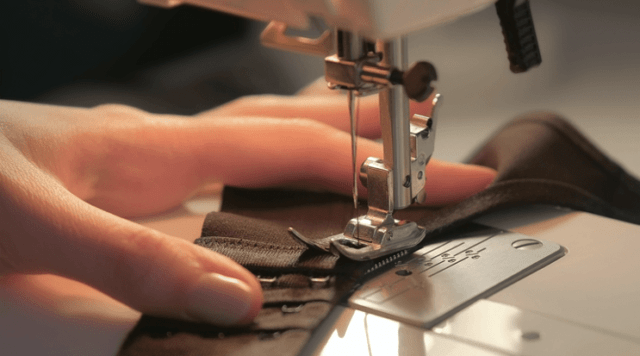
#ProductionPlanning
Intimark uses FastReactPlan to improve operational efficiency
World class intimates and sports apparel manufacturer implements FastReactPlan to support speed programs and improve visibility, coordination and control, providing…
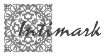