GSDCost implementation is the catalyst for change at Sabrina
By using GSDCost, the innovative garment manufacturer, has increased productivity efficiencies by 15% as well as significantly improving methods.
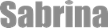
Sabrina was founded in 1974 and have its headquarters in New Taipei City, Taiwan. They have garment manufacturing facilities in Taiwan, China, Cambodia, Vietnam, and Myanmar. Sabrina commits itself to the innovation and production of performance apparel and is now one of the largest producers in the global supply chain.
They produce high-quality apparel including cycling apparel, training apparel, protective base layer, tennis clothing, golf garments, etc.
Their innovation capability in garment production, attention to quality, and timely delivery have earned the business a distinctive reputation within the industry. The capabilities and effectiveness of the management have been elevated as the GSDCost projects made the whole process of change more objective, measurable and enhanced communication within the internal team. Companies who implement GSDCost see increased productivity efficiencies and also method improvements. Sabrina soon experienced both of these benefits:
1. Catalyst for change – Increased productivity efficiency
Sabrina has seen an elevation of their productivity efficiencies of between 10% and 15%. Establishing accurate and optimised efficiencies within a garment manufacturing unit ensures more consistent and relevant data for use in fact-based costing, line balancing, and production planning, with known capacities.
2. Catalyst for change – Method improvement
Since introducing GSDCost into their business the team of trained and qualified GSD practitioners at Sabrina now see and think in the language of human motion.
This, together with a commitment to Lean Manufacturing Excellence, has enabled Sabrina to identify and reduce waste within their production units, which was present within the methods used before the GSDCost implementation. Additionally, through the introduction of detailed method standards, quality is improved as their processes now have increased consistency with less method variability.
Related testimonials
Americas
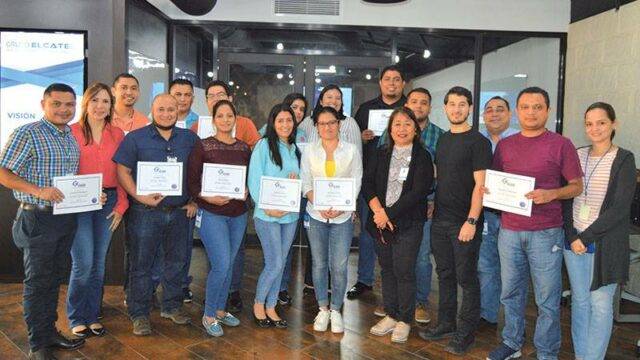
#MethodTimeCostOptimisation
Elcatex Group adopts GSDCost to optimise garment costing
The vertically-integrated manufacturer from Honduras chose GSDCost to quantify and optimise manufacturing methods and garment costing, as a part of…

South Asia
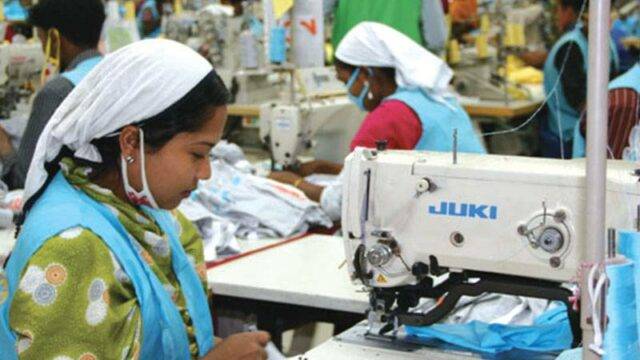
#MethodTimeCostOptimisation
GSDCost gives Epyllion transparency of their true cost of production
Epyllion now has the tools to set meaningful production targets based on fact-based capacity data. Additionally, the lost business opportunities,…
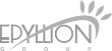
South East Asia
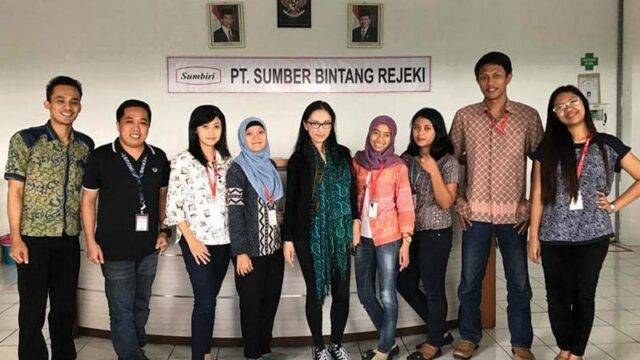
#MethodTimeCostOptimisation
PT. Sumbiri boosts productivity by 13% with GSDCost
The introduction of GSDCost allowed PT. Sumbiri to create accurate method standard for production to help them establish and optimise…
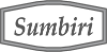